Pt. 1: How Real-Time Visualization is Revolutionizing Manufacturing Operations
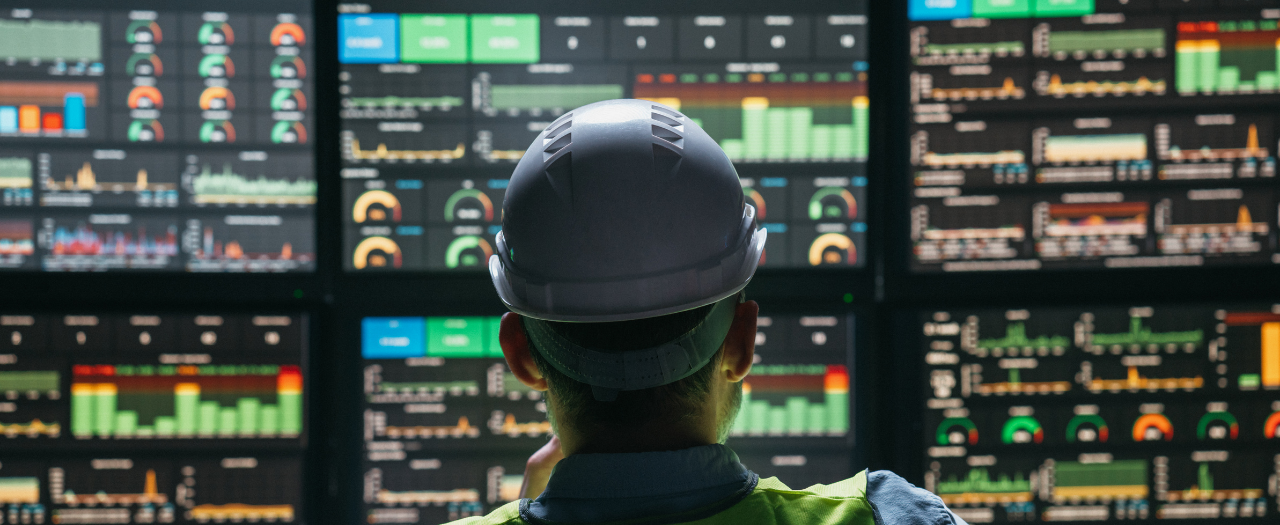
The manufacturing landscape is evolving faster than ever. As global competition tightens and consumer demands shift, organizations are under immense pressure to boost productivity, cut costs, and deliver products more quickly—all without compromising on quality. Meeting these challenges head-on requires more than just advanced machinery; it calls for smarter, data-driven processes. Real-time data visualization has emerged as the answer to meet the demands of this transformation, turning the chaos of raw information into actionable dashboards, charts, and heat maps. Let’s explore why this shift matters and how it’s enabling factories to operate at the peak of efficiency.
Why Real-Time Matters
In many factories, vital information is hidden in spreadsheets, siloed databases, or manual logs. These snapshots of historical data are only valuable once the shift has ended or the week has passed—and by then, the opportunity to address an emerging issue has already slipped away. Real-time visualization tools change the game by removing this time lag. Instead of reacting to problems after they grow, teams can take proactive measures in the moment.
Furthermore, real-time monitoring keeps everyone aligned. From machine operators on the floor to managers in the control room, a unified, up-to-date perspective helps each stakeholder make decisions based on the same data. This immediacy reduces miscommunication and drives rapid, coordinated responses to changing conditions on the production line.
Centralized Dashboards for Seamless Oversight
At the heart of real-time visualization are centralized dashboards that gather key performance indicators (KPIs) from multiple sources. Manufacturing Execution Systems, quality control data, even IoT sensors mounted on equipment—all feed into a single interface. In a factory setting, it’s crucial to know how these data points connect. For example, monitoring throughput alongside energy usage can reveal efficiency gaps that might be overlooked when each metric is tracked in isolation.
Dashboards typically feature customizable widgets or tiles that spotlight critical metrics: machine uptime, scrap rates, yield, and more. Automatic alerts, triggered when metrics deviate from set thresholds, allow managers to take immediate corrective action. This is especially useful for high-volume production lines, where even a minor issue can translate into substantial waste if not caught early. However, with all of this technological flexibility it is important to remember that there are the rare chances it may fail us in some way, but using this technology is the best way to prepare for the future.
A Cultural Shift: Empowering Teams
The advent of real-time data visualization has also triggered a shift in workplace culture. Operators, once dependent on static reports, can now see how their actions affect key metrics in the moment. This immediate feedback loop encourages autonomy and shared responsibility. Engineers can adjust machine parameters based on real-time alerts, accelerating continuous improvement efforts. Meanwhile, managers can use live dashboards to coach teams or reallocate resources as needed.
Moreover, cloud-enabled dashboards allow remote collaboration. Engineers in different locations can access the same real-time views as on-site personnel, offering guidance or diagnosing issues from anywhere in the world. This connectivity opens doors to new workflows and business models that were previously impossible or cost prohibitive.
Real-time visualization is revolutionizing how manufacturing operations are managed and optimized. By unifying data from multiple sources into visually rich dashboards, charts, and heat maps, factories can respond to challenges as they unfold and seize opportunities for continuous improvement. Whether it’s pinpointing process bottlenecks, tailoring preventive maintenance, or driving cultural change through data transparency, real-time visualization stands out as the linchpin of the modern manufacturing era. Embracing these tools isn’t just a matter of staying competitive—it’s about defining the new frontier for operational excellence.
Our expert team is here to help you implement the best solutions tailored to your unique needs. Find out more about our Automation and Manufacturing solutions.