Pt. 2: How Real-Time Visualization is Revolutionizing Manufacturing Operations
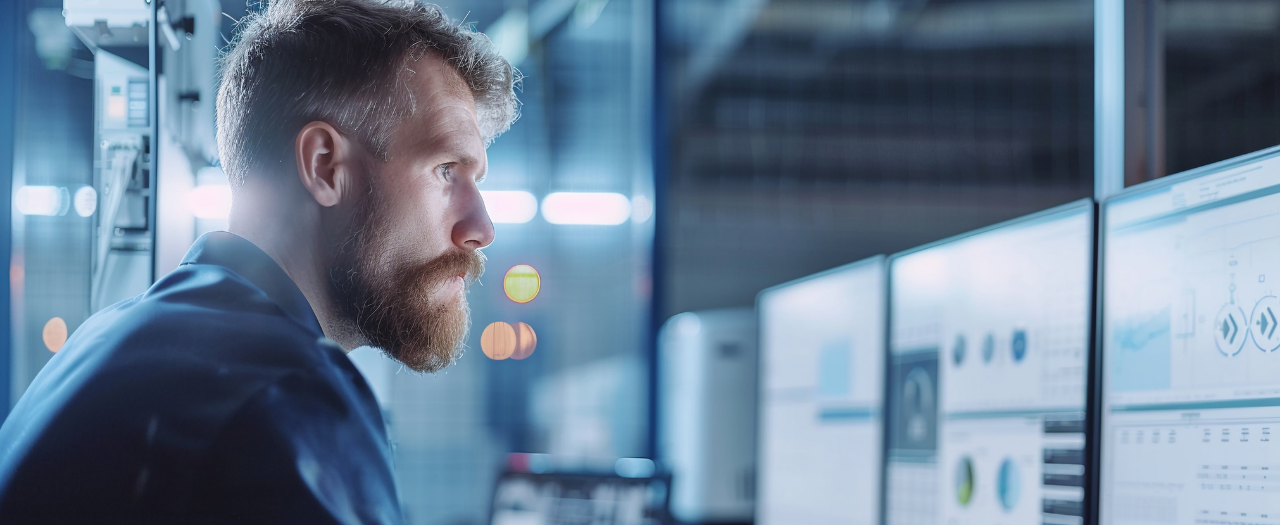
How to Optimize and Surpass Standard BI Tools
While traditional business intelligence solutions can be useful for general reporting, manufacturers often need more specialized or flexible visualization approaches. Factories typically draw data from an array of industrial systems and protocols. But real-time visualization technologies dramatically improve the performance by allowing developers or process engineers to integrate data from multiple platforms—like supply chain management systems, sensor networks, and REST API endpoints—provide a far more holistic view.
Such flexibility is invaluable. An on-premises production database can be instantly combined with cloud-based analytics for machine performance. Once consolidated, these sources feed directly into custom dashboards that reflect how a particular manufacturing operation actually runs, rather than forcing processes to adapt to rigid, out-of-the-box software solutions.
Charts, Graphs, and Heat Maps: Translating Numbers into Insights
Large volumes of data can be overwhelming without the right visual context. Charts, graphs, and heat maps transform raw figures into intuitive illustrations. A trend chart might show how production throughput correlates with energy consumption, giving teams a quick indication of efficiency gains or losses. Pie charts and bar graphs can break down quality metrics or defect rates by production line, shift, or batch number, enabling instant comparisons.
Heat maps are particularly powerful for spatial insights. By overlaying data onto a 2D factory layout—or a 3D model—teams can quickly identify where material flow slows, storage areas jam up, or work-in-progress queues accumulate. These visual cues not only highlight bottlenecks but also suggest ways to streamline layouts, reduce transportation waste, and improve worker ergonomics.
Preventive and Predictive Maintenance
Real-time visualization doesn’t stop at productivity metrics—it also supercharges maintenance strategies. Sensors embedded in machinery can continuously relay information about temperature, vibration, or component wear. By displaying these readings in real time, dashboards provide early warning signs of equipment stress or imminent failure.
Preventive maintenance schedules can be planned around actual machine conditions instead of generalized timelines. Over time, advanced analytics layered onto these dashboards can also predict future breakdowns. Proactive fixes help factories avoid unplanned downtime, which can cost thousands of dollars an hour in lost production. Instead, maintenance interventions can be strategically scheduled during lulls or shift changes, minimizing disruptions.
Real-time visualizations are already changing the name of the game on manufacturing floors—implementing it sooner rather later will only put you ahead of the game.
Our expert team is here to help you implement the best solutions tailored to your unique needs. Find out more about our Data Visualization solutions. Read part 1 here.